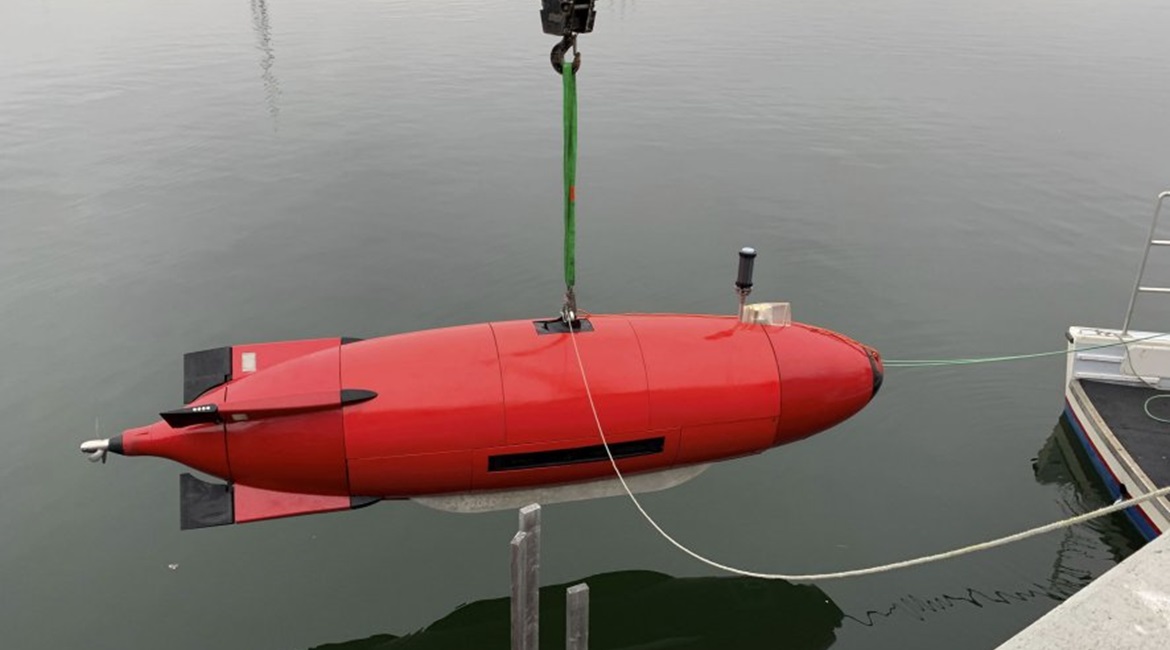
Massachusetts-based startup Dive Technologies is looking to leverage additive manufacturing (AM) technologies, commonly referred to as 3D printing, for large and extra-large unmanned underwater vehicle (UUV) applications.
Dive Technologies utilised a Cincinnati Incorporated Big Area Additive Manufacturing (BAAM) 3D printer for the external hull fairings and smaller 3D printers for the internal components of their DIVE-LD autonomous underwater vehicle (AUV). BAAM is an industrial-grade 3D printer that uses an extruder placed on a gantry system to create parts using materials such as high-performance thermoplastics, engineering grade thermoplastics, consumer grade thermoplastics and additives.

DIVE-LD AUV being lowered into the water for a trial. (Dive Technologies)
According to the company, BAAM features dynamic flow control, precise melt temperature control, and proprietary bead tamping technology, which enables it to print fully fused parts with consistent bead widths and minimal porosity. The system is also equipped with a large extruder and a high-speed motion system that provides it an extrusion rate of 36 kg/hour.
Dive Technologies co-founder Bill Lebo told Janes in late March that they originally planned to use thermoformed plastics for the external hull fairings for the DIVE-LD AUV.
To drive down the cost of the vehicle, Dive Technologies established a co-operative research and development agreement with Oak Ridge National Laboratory (ORNL), spending about two years investigating large format additive manufacturing (LFAM) technology to create the fairings for their first DIVE-LD AUV. During the process, the manufacturer realised the potential of LFAM to rapidly produce finished, customised components without the need for expensive tooling that the industry had become accustomed to.
Looking to read the full article?
Gain unlimited access to Janes news and more...